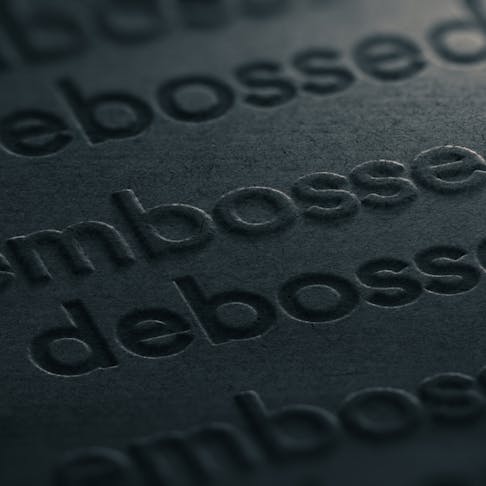
Debossing: Definition, Process, Materials, and Types
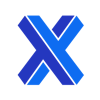
Debossing is one of many various techniques that are employed to enhance the visual appeal of a product. Debossing is the process of pressing a die into a material to create a sunken image that adds depth and texture to products.
This article delves into the intricacies of debossing and explores its definition, process, materials, types, advantages, disadvantages, and more.
What Is Debossing?
Debossing is a process in which a design is depressed or imprinted into a material’s surface. Many different types of debossing are suitable for a variety of materials: paper, fabric, leather, and metal. Regardless of the type, debossing uses a metal die to imprint the design or image into the material. This process heightens the aesthetic appeal of the material as it leaves a tactile and visually appealing feature.
What Is the Process of Debossing?
The process of debossing typically involves several steps which are described below:
- Create the die or mold that carries the desired design or image to be debossed. Precision and attention to detail are critical to ensuring the impression created by the die accurately meets the design requirements. CNC machining or laser cutting are two manufacturing methods typically used for fabricated debossing dies composed of various metals.
- Place the fabricated die or mold in a press machine and heat it to help imprint the pattern or image into the material. The increased die temperature helps soften the material to make it more pliable and receptive to the debossing process. The material to be debossed is placed under the press, aligned in position, and fixed to prevent movement during the debossing process.
- The press and die assembly lowers and exerts significant force into the material to create an impression in the material.
- After the pattern is imprinted into the material, allow time for the material to cool (and in some cases harden) if necessary. After sufficient cooling, the material can be removed from the press.
What Is the Use of Debossing?
Debossing finds applications across various industries, including: packaging, branding, stationery, and fashion. It is commonly used to add logos, text, or decorative elements to products like: business cards, flyers, wallets, and handbags to enhance their visual appeal and perceived value.
What Are the Materials That Can Be Debossed?
Debossing is a versatile technique that can be applied to a wide range of materials. Applicable materials are listed below:
1. Wood
Wood is a versatile material that can be debossed to create unique textures and patterns. Debossing in wood is commonly used for: crafting, woodworking, and furniture for decorative purposes.
2. Paper
Paper is one of the most common materials for debossing due to its flexibility and availability. It is often used for debossed elements on products such as: stationery, invitations, and packaging. To learn more, see our full guide on Paper.
3. Fabric
Fabric can be debossed to add texture and visual interest to clothing, accessories, and upholstery. Debossed fabric is commonly used in: fashion design, home decor, and textile industries.
4. Plastic
Plastic materials, such as: PVC, acrylic, and polycarbonate, can be debossed to create durable and long-lasting designs. Debossed plastic is often used in: signage, product branding, and industrial applications.
5. Cardboard
Cardboard is frequently debossed to add dimension and tactile appeal to packaging, displays, and promotional materials. Debossed cardboard is lightweight, cost-effective, and eco-friendly.
6. Foam
Foam materials, such as EVA foam and polyethylene foam, can be debossed to create cushioned surfaces with customized patterns and textures. Debossed foam is commonly used in athletic padding, protective gear, and packaging inserts.
7. Leather
Leather is a popular material for debossing due to its durability and luxurious appearance. Debossed leather is commonly used in leather goods such as: wallets, belts, bags, and footwear.
8. Rubber
Rubber materials, including both natural rubbers and synthetic rubbers, can be debossed to create flexible and resilient designs. Debossed rubber is used in applications such as: seals, gaskets, and industrial components.
9. Metal
Metals like aluminum, brass, and stainless steel, can be debossed to create durable and high-precision designs. Debossed metal is commonly used in: signage, nameplates, and decorative accents.
10. Composite Materials
Composite materials, such as fiberglass-reinforced plastics (FRP) and carbon-fiber composites, can be debossed to achieve lightweight and high-strength designs. Debossed composite materials are used in: aerospace, automotive, and sporting goods industries.
What Machine Is Used in Debossing?
Debossing is often performed using specialized machinery known as debossing machines or presses. These machines apply pressure evenly across the die, ensuring precise and consistent results. Some debossing machines have integrated heating elements that heat the die or mold to the required temperature. If this feature is not available, a heat gun may be used to heat the die.
What Are the Different Types of Debossing?
Many different types of debossing are utilized to satisfy different product requirements. The different types of debossing are listed below:
1. Blind Debossing
Blind debossing involves pressing the design into the material without the use of ink or foil. Without additional materials like ink or foil, blind debossing can lead to deeper imprints which help create a subtle, yet elegant effect. Blind debossing is often used for materials like: paper, fabric, leather, cardboard, and some plastics.
2. Registered Debossing
Registered debossing is a type of debossing that merges printing with debossing. In registered debossing, the design or pattern is printed with ink onto the material. Then, the die is precisely aligned with the printed element and pressed into the part. The process creates a textured, three-dimensional effect. Registered debossing is commonly used to create logos, packaging, and elegant design features in luxury goods.
3. Embossed and Debossed Combination (Combo or Dual Debossing)
Combo debossing combines both embossing and debossing to create intricate designs with contrasting textures. Compatible materials include: paper, cardboard, fabric, and some plastics to create elegant stationery, high-end packaging, fashion design, and more.
4. Foil Stamping With Debossing
In foil stamping with debossing, foil is applied to the material before debossing. When the die is pressed into the material, the desired imprint is indented into the material and has a metallic finish. Foil stamping with debossing is often used with paper, cardboard, and leather for luxury packaging and stationery, premium leather goods, and promotional materials.
5. Multi-Level or Sculptured Debossing
Multi-level or sculptured debossing is a process in which multiple depths are created within the design to add dimension and complexity. Sculptured debossing is used with paper, fabric, cardboard, and leather to create intricate textures and embellishments in parts.
How To Choose What Type of Debossing to Use?
Choosing the debossing technique most suitable for a project depends on factors such as: the desired aesthetic, material properties, and budget constraints. For example, blind debossing may be preferred for a minimalist look, while foil stamping with debossing can lend a luxurious feel to the product.
What Industries Use Debossing?
Debossing is utilized across various industries—from luxury goods and fashion, to publishing and packaging, to stationery and paper. It is commonly seen on items such as: business cards, book covers, leather goods, and product packaging.
What Is the Advantage of Debossing?
The advantages of debossing are listed below:
- Depth and Dimension: Debossing adds depth and dimension to materials by physically altering the material’s surface rather than simply adding color. This tactile quality enhances engagement and visual appeal which makes debossing ideal for items like business cards or promotional materials.
- Durability: The imprinted design in debossing is durable and less prone to fading or wearing away over time. This durability is particularly beneficial for frequently handled items such as business cards or leather goods.
- Precision and Detail: Custom-made dies allow for highly detailed and intricate designs in debossing. This precision makes it suitable for applications requiring intricate patterns or detailed logos.
What Is the Disadvantage of Debossing?
The disadvantages of debossing are listed below:
- Cost: Debossing can be more expensive than other printing techniques due to the need for custom-made dies. The cost impact becomes more pronounced for smaller print runs and complex designs.
- Limitations in Color: Debossing is limited in terms of color as it involves pressing a design into the material's surface. While color can be added separately in an additional process, this increases the project's cost and complexity.
- Material Suitability: While debossing can be applied to various materials, not all materials are suitable. Thin or fragile materials may tear or distort under the pressure, while hard or brittle materials may crack or break during the debossing process.
How Does Debossed Design Depth Affect Product Appearance and Feel?
The depth of the debossed design can significantly impact the product's appearance and feel. Deeper impressions tend to create a more pronounced tactile effect, while shallower debossing may result in a subtler texture.
What Is the Difference Between Embossing and Laser Engraving?
Embossing involves creating raised designs on a material's surface, while laser engraving involves removing material to create a design. Additionally, embossing is typically done using dies or molds while laser engraving utilizes laser technology to create designs in materials.
What Is the Difference Between Embossing and Debossing?
The primary difference between embossing and debossing is the direction of the imprinted design. Embossing is a process that raises the desired design above the material's surface, while debossing presses the design into the material to create a sunken effect.
Summary
This article presented debossing, explained it, and discussed its process and the various materials that can be used. To learn more about debossing, contact a Xometry representative.
Xometry provides a wide range of manufacturing capabilities, including stamping and other value-added services for all of your prototyping and production needs. Visit our website to learn more or to request a free, no-obligation quote.
Disclaimer
The content appearing on this webpage is for informational purposes only. Xometry makes no representation or warranty of any kind, be it expressed or implied, as to the accuracy, completeness, or validity of the information. Any performance parameters, geometric tolerances, specific design features, quality and types of materials, or processes should not be inferred to represent what will be delivered by third-party suppliers or manufacturers through Xometry’s network. Buyers seeking quotes for parts are responsible for defining t
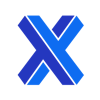